振动时效工艺在精密冷拔钢管生产过程中的研究与应用
0、 引言
应用振动消除金属构件或特殊加工后金属内部的应力(代替热时效或自然时效),这类新技术在国外被称作:“Vi-bratory Stress Relief”简称(VSR)。作为一种新型的消除金属内部应力的方法,它具有节省能源、缩短生产周期、操作简便等优点。
成都无缝钢管公司于2006年开始进行振动时效新工艺在精密冷拔钢管生产过程中的应用与研究,取得了良好的效果。应用振动时效新地冷拔钢管进行消除应力处理,取代了加工过程中的回火处理工序,缩短应力消除的时间,提高生产效率。精密冷拔钢管生产技术其加工原理是将普通的无缝钢管在外力的作用下,使壁厚发生塑性变形,达到所需尺寸和精度,实现加工目的。它具有节省材料、快速成型、提高被加零件的机械性能、投资少等优点。但也存在一些缺陷,表现在冷拔过程中产生较大的内应力(简称残余应力),它对冷拔后钢管尺寸的稳定、综合机械性能产生不利的影响,甚至在使用过程中出现爆裂现象,限制了精密冷拔钢管的使用,如何快速消除冷拔过程中产生的残余内应力,是生产过程中的一大难题。
1、 振动时效处理的机理分析
振动时效是基于谐波共振原理,把频率在一定范围内连续可调的激振器,固定在被振工件适当的位置,通过激振力和频率的调整,迫使工件在一定周期性外力作用下在共振频率范围内产生振动,经过一定时间后,即可达到降低、均化残余应力,稳定尺寸的效果。
这种外加的周期性循环动力应满足:δ动+δ残≥δS
式中 δ动———激振器施加给工件的周期性动应力;
δ残———工件的残余应力;
δS———工件材料的屈服极限。
这样振动作用力与残余应力之和达到工件材料屈服极限时就产生塑性变形,使工件中原有的不稳定的残余应力得到松弛和均化,残余应力得到调整,从而强化了基体,使工件的几何尺寸趋于稳定。
2 时效处理应用前的工艺性试验
2•1 概况
成都无缝钢管公司加工精密冷拔钢管的原材料均采用:27SiMn无缝钢管;直径在φ50~φ300 mm之间、长度在5~10•5 m之间;每次拔制时钢管壁厚的变形量控制在0•5~5mm之间,拔制次数在3~4次。在初拔过程中变形量较大,内应力集中,此时若不进行回火或其它去应力处理,对后期的拔制产生不利影响,主要表现在断裂、拔偏、拉痕、尺寸不稳定等。为解决上述问题,该公司曾试验过在冷拔工序后增加回火去应力的方法,取得了一定的效果,但耗能大、环境污染、延长了生产周期,特别是随着10 m以上加长管生产任务的加大,对回火炉提出了更高的要求。
2•2 工艺性试验路线的制定
该公司工艺技术人员选取了几种常用的不同规格、长度、壁厚的无缝钢管进行了2种时效方法的工艺性试验,并制定了具体的工艺路线。
冷拔→振动时效(热时效)→精拔→锯断→珩磨→精度测量
3 振动时效的参数选择
3•1 激振频率的选择
原则:能耗小振幅大,动态参数曲线的变化规律保持为上升型,这样便于振动时对效果的鉴别。
在选择频率的实际操作中,是先将振动时效处理仪选择自动扫描,扫出振幅最大处所对应的频率,然后在亚共振动区,即g=(1/3~2/3)gmax为共振频率,这样确定激振频率,根据试验表明该方法方便、快捷;同时还可避免激振频率选择不当造成的应变硬化和疲劳损坏。
3•2 激振力(动应力)的选择
激振力的选择应以工件上最大的动应力来确定,只需满足δ动+δ残≥δS即可。但对工件的残余应力测定有一定的困难,无法快速检测时,通过试验和分析可用如下的经验公式:δ动=2/3δS,应用效果还可以。
3•3 振动时间的确定
原则:应根据被振动工件的金属特性、体积等一些因素来确定。
通过对不同规格和冷拔次数的冷拔管的振动曲线分析后发现:残余应力变化最快的是在振动处理前的5 min左右,15 min以后基本趋于稳定,说明当工作的残余应力降到一定程度以后,就不再发生大的变化,因此一般激振时间选定在20 min左右。
3•4 工件支承及装夹选择
在振动时效处理时,激振器的安装位置和固定方式有一定的要求,实践中发现将激振器坚固在工件的中间处,(同时振动多件时采用整体夹紧的方式)用弹性垫块支承在波节(或称节线处)即金属工件在自由振动时振幅最小处,效果最为明显。
4 振动时效的试验及结果分析
采用的是济南西格马科技有限公司生产的振动时效系统,转速范围2 000~10 000 rpm,最大激振力可达15 kN,最大功率为1 200W;试验工件为:外径为φ114 mm,内径为φ92 mm;长度10 m的冷拔管。先进行扫频,画出特性曲线1,找出其谐振频率,然后选择亚共振区频率,用适当的激振力进行振动时效20min,振后再次画出扫频特性曲线2,见图1。
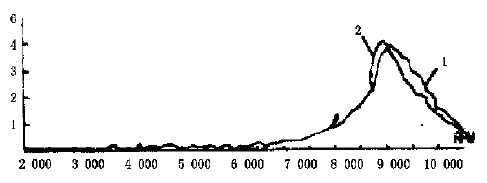
通过比较振前曲线1,振后曲线2,可以看出:曲线2对曲线1峰值频率左移,幅值也有增加,另外特性曲线2的幅值随着振动时间的延长,趋于稳定。由此可以判断和分析出振动时效处理工艺效果是较良好。为进一步验证上述的结论,我们将5根冷拔后的工件从中间锯断,工件进行两种时效方法的处理,然后测量其静态直线度,具体数据如表1。
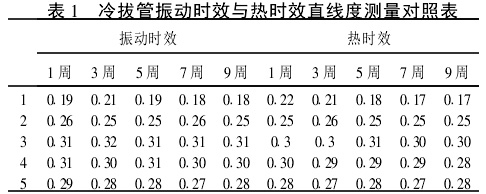
根据以上数据的分析对比,可以看出振动时效与热时效其效果比较接近,并且均符合允差范围,经振动时效的试件,它在直线度稳定性方面略好于热时效处理。经分析,这可能是由于退火炉内温度分布不均匀及试件放置的正确性等因素所致。
5 效益分析
采用热时效每吨费用大约为150元(指燃煤炉),而采用电炉费用更高,振动时效激振器功率不到1200 W,耗能只是热时效的1%~3%,可节省大量能源。
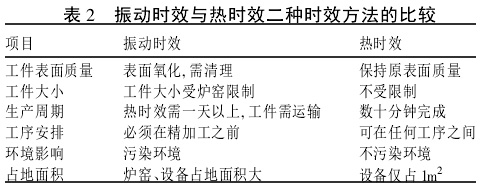
6 结束语
经过几年的摸索,特别是通过大量的试验及实践表明振动时效技术是行之有效的,对精密冷拔钢管的处理同热时效处理基本相同。另外,振动时效并不能完全代替热时效,通过对两者的显微结构分析,振动时效不能改变热影区的组织及性能,对于冷拔次数较多,淬硬性较大材料应用振动时效会出现裂纹、断裂等现象,还必需用热时效改善组织性能。
应用振动消除金属构件或特殊加工后金属内部的应力(代替热时效或自然时效),这类新技术在国外被称作:“Vi-bratory Stress Relief”简称(VSR)。作为一种新型的消除金属内部应力的方法,它具有节省能源、缩短生产周期、操作简便等优点。
成都无缝钢管公司于2006年开始进行振动时效新工艺在精密冷拔钢管生产过程中的应用与研究,取得了良好的效果。应用振动时效新地冷拔钢管进行消除应力处理,取代了加工过程中的回火处理工序,缩短应力消除的时间,提高生产效率。精密冷拔钢管生产技术其加工原理是将普通的无缝钢管在外力的作用下,使壁厚发生塑性变形,达到所需尺寸和精度,实现加工目的。它具有节省材料、快速成型、提高被加零件的机械性能、投资少等优点。但也存在一些缺陷,表现在冷拔过程中产生较大的内应力(简称残余应力),它对冷拔后钢管尺寸的稳定、综合机械性能产生不利的影响,甚至在使用过程中出现爆裂现象,限制了精密冷拔钢管的使用,如何快速消除冷拔过程中产生的残余内应力,是生产过程中的一大难题。
1、 振动时效处理的机理分析
振动时效是基于谐波共振原理,把频率在一定范围内连续可调的激振器,固定在被振工件适当的位置,通过激振力和频率的调整,迫使工件在一定周期性外力作用下在共振频率范围内产生振动,经过一定时间后,即可达到降低、均化残余应力,稳定尺寸的效果。
这种外加的周期性循环动力应满足:δ动+δ残≥δS
式中 δ动———激振器施加给工件的周期性动应力;
δ残———工件的残余应力;
δS———工件材料的屈服极限。
这样振动作用力与残余应力之和达到工件材料屈服极限时就产生塑性变形,使工件中原有的不稳定的残余应力得到松弛和均化,残余应力得到调整,从而强化了基体,使工件的几何尺寸趋于稳定。
2 时效处理应用前的工艺性试验
2•1 概况
成都无缝钢管公司加工精密冷拔钢管的原材料均采用:27SiMn无缝钢管;直径在φ50~φ300 mm之间、长度在5~10•5 m之间;每次拔制时钢管壁厚的变形量控制在0•5~5mm之间,拔制次数在3~4次。在初拔过程中变形量较大,内应力集中,此时若不进行回火或其它去应力处理,对后期的拔制产生不利影响,主要表现在断裂、拔偏、拉痕、尺寸不稳定等。为解决上述问题,该公司曾试验过在冷拔工序后增加回火去应力的方法,取得了一定的效果,但耗能大、环境污染、延长了生产周期,特别是随着10 m以上加长管生产任务的加大,对回火炉提出了更高的要求。
2•2 工艺性试验路线的制定
该公司工艺技术人员选取了几种常用的不同规格、长度、壁厚的无缝钢管进行了2种时效方法的工艺性试验,并制定了具体的工艺路线。
冷拔→振动时效(热时效)→精拔→锯断→珩磨→精度测量
3 振动时效的参数选择
3•1 激振频率的选择
原则:能耗小振幅大,动态参数曲线的变化规律保持为上升型,这样便于振动时对效果的鉴别。
在选择频率的实际操作中,是先将振动时效处理仪选择自动扫描,扫出振幅最大处所对应的频率,然后在亚共振动区,即g=(1/3~2/3)gmax为共振频率,这样确定激振频率,根据试验表明该方法方便、快捷;同时还可避免激振频率选择不当造成的应变硬化和疲劳损坏。
3•2 激振力(动应力)的选择
激振力的选择应以工件上最大的动应力来确定,只需满足δ动+δ残≥δS即可。但对工件的残余应力测定有一定的困难,无法快速检测时,通过试验和分析可用如下的经验公式:δ动=2/3δS,应用效果还可以。
3•3 振动时间的确定
原则:应根据被振动工件的金属特性、体积等一些因素来确定。
通过对不同规格和冷拔次数的冷拔管的振动曲线分析后发现:残余应力变化最快的是在振动处理前的5 min左右,15 min以后基本趋于稳定,说明当工作的残余应力降到一定程度以后,就不再发生大的变化,因此一般激振时间选定在20 min左右。
3•4 工件支承及装夹选择
在振动时效处理时,激振器的安装位置和固定方式有一定的要求,实践中发现将激振器坚固在工件的中间处,(同时振动多件时采用整体夹紧的方式)用弹性垫块支承在波节(或称节线处)即金属工件在自由振动时振幅最小处,效果最为明显。
4 振动时效的试验及结果分析
采用的是济南西格马科技有限公司生产的振动时效系统,转速范围2 000~10 000 rpm,最大激振力可达15 kN,最大功率为1 200W;试验工件为:外径为φ114 mm,内径为φ92 mm;长度10 m的冷拔管。先进行扫频,画出特性曲线1,找出其谐振频率,然后选择亚共振区频率,用适当的激振力进行振动时效20min,振后再次画出扫频特性曲线2,见图1。
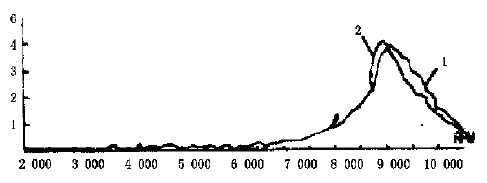
通过比较振前曲线1,振后曲线2,可以看出:曲线2对曲线1峰值频率左移,幅值也有增加,另外特性曲线2的幅值随着振动时间的延长,趋于稳定。由此可以判断和分析出振动时效处理工艺效果是较良好。为进一步验证上述的结论,我们将5根冷拔后的工件从中间锯断,工件进行两种时效方法的处理,然后测量其静态直线度,具体数据如表1。
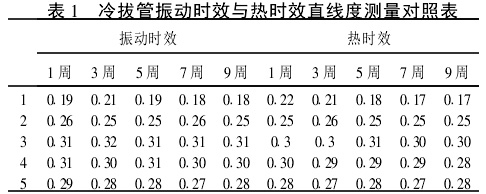
根据以上数据的分析对比,可以看出振动时效与热时效其效果比较接近,并且均符合允差范围,经振动时效的试件,它在直线度稳定性方面略好于热时效处理。经分析,这可能是由于退火炉内温度分布不均匀及试件放置的正确性等因素所致。
5 效益分析
采用热时效每吨费用大约为150元(指燃煤炉),而采用电炉费用更高,振动时效激振器功率不到1200 W,耗能只是热时效的1%~3%,可节省大量能源。
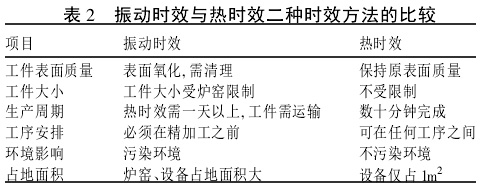
6 结束语
经过几年的摸索,特别是通过大量的试验及实践表明振动时效技术是行之有效的,对精密冷拔钢管的处理同热时效处理基本相同。另外,振动时效并不能完全代替热时效,通过对两者的显微结构分析,振动时效不能改变热影区的组织及性能,对于冷拔次数较多,淬硬性较大材料应用振动时效会出现裂纹、断裂等现象,还必需用热时效改善组织性能。